Matt, this is a Sunday afternoon spring compressor I built for my HT. It's something like what Tony and We-wreck mentioned. It should, in principle, work on your HJ.
Mine is M12 allthread, with a kink at the bottom of about 15 degrees. Because the lower control arm pivots and changes angle as it compresses the spring you need to allow for a swivel on the bottom to avoid bending the allthread bar. I've used a Chev rocker arm pivot ball in a suitable hole in the bottom plate to allow for the change in bottom arm angle as you tension the spring.
Note the thick oversized washers, just in case the pivot ball pulls through the bottom plate, and the double nuts at each end. As you tension the spring, keep the safety nut within a turn or two of the tension nut.
there is also a large ring on the bottom portion to fit in a recess in the lower control arm on HT, which I've since tack welded onto the bottom plate. Your lower control arm is different, and may need a slightly different arrangement. The bottom plate is 4mm. There is also a step washer I made on the top, the smaller diameter of which fits into the shock absorber hole in the spring tower. All of this is to centre the allthread bar in the top shock absorber hole, and the larger hole in the lower control arm and avoid using the allthread as a low speed milling machine, damaging the holes through which it passes. I also didn't want to scratch the paint!
If you can only get galvanised allthread, wire brush the galvanising off each end of it, and/or run a die nut over the thread. Galvanising is a rough surface finish, and the last thing you need when you tighten this up is excess friction. For the same reason, use plated nuts, and not galvanised ones. Use plenty of lubricant, such as WD40 spray, as you tighten it up.
Common or garden variety allthread is good for about 400Mpa tensile stress, so a piece of M12 allthread will take a tensile load of about 3400kg, and M16 about 6400kg.
If your spring has a rate of 700 lb/inch (a guess) and you need to compress it 3 inches (another guess) you will have a load of about 950kg in your allthread, which is safe for both M12 and M16.
When you tension it, keep well clear of the lower control arm, and the area where the spring will exit the front end should anything let go. It's never happened to me, but the compressed spring has a large amount of stored energy, which you do not want to absorb with your soft bits.
Good luck,
Geoff
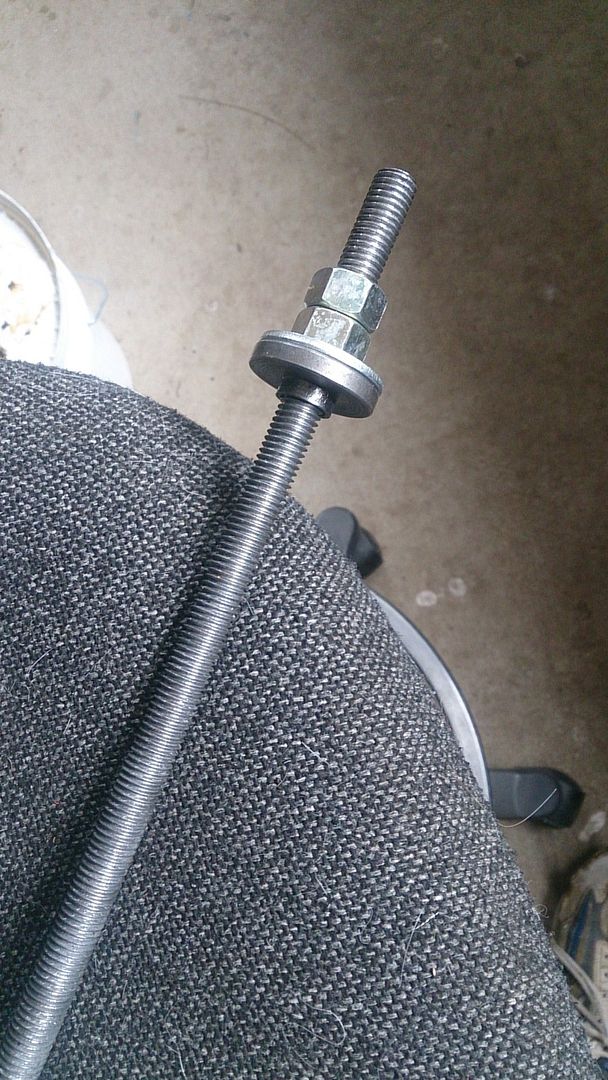

